Aerodynamic Efficiency Project
Aerodynamics
Oct. 2021 - Dec. 2021
Technical Skills: Autodesk Inventor, Autodesk CFD
​
Objective: Design parts to improve the aerodynamic efficiency of a semi-trailer truck
About:
The final project for my Aerodynamics course was a test in improving aerodynamic efficiency. Each group of students was given the same initial design of a semi-truck. The teams were given four areas of focus: the space between the cab and the trailer, the end of the trailer, the top of the cab, and the front of the cab. The goal was to design parts to be added to the truck which would reduce the amount of drag on the truck. Using Autodesk Inventor to design the parts and Autodesk CFD to test their effects on the drag, each team came up with improved truck design and presented to the class and professor.
Lessons Learned:
This project allowed me to grow my foundation in Autodesk CFD. I was already fairly strong in CAD modeling (Inventor) but had much less experience using CFD. I had gotten some practice in extra curriculars but this was the first course where I learned to use this software and by doing this project I was able to get a much more firm grasp on it. I enjoyed testing my ideas and interpreting the results and learned that some ideas work well on their own but when coupled with others they may interfere with one another. This taught me the importance of continuous testing rather than assuming that something that worked once or in one situation will always work.
​

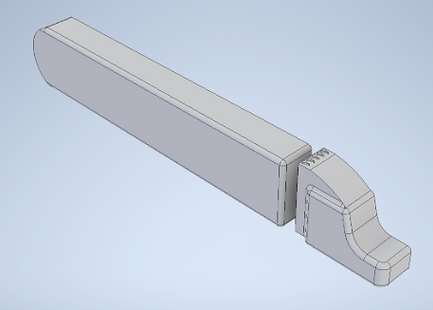
Contributions:
Each of my four group members chose one area of focus. My focus area was the end of the trailer. The top image (a mesh and gradient display of velocity from Autodesk CFD) displays the initial truck design. Behind the trailer is an area of solid dark blue, the darkest color present in the gradient. This indicates a region of very low velocity, if not zero velocity. This meant that the air was not flowing behind the trailer and large amounts of drag were being produced. To solve this issue, I designed a bubble to add to the end of the trailer. Rounding the corners and giving a slower transition allowed the air to remain attached to the surface for longer and maintain a more laminar, fast-moving flow. I designed this part and used Autodesk CFD to test multiple iterations of it with differing sizes.
When each of my teammates found the best solution to the drag in their focus area, they sent me their part designs and I assembled our final truck configuration (seen in the second image above). We ran our final design in CFD and presented our results to the class.